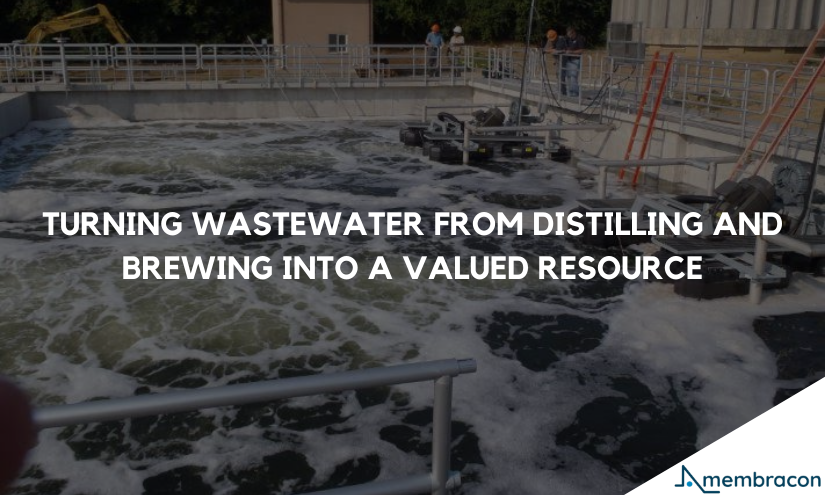
Turning wastewater from distilling and brewing into a valued resource
Water is crucial for distillation and brewing, but most of it ends up as wastewater. Distillers and brewers are tasked with reducing their water footprint without compromising production capacity. A potential solution lies in seeing wastewater as a valuable commodity rather than something to tip down the drain.
Most wastewater from distillation and brewing is suitable for recovery and treatment to return it to a quality suitable for other applications.
For example, treated wastewater is suitable for cleaning and washing facilities, boiler feed water, and cooling processes.
No matter how saturated and contaminated wastewater is, it only requires the correct treatment to purify it. Several cycles and technologies are often required, but recovering wastewater is always possible.
Finding value in wastewater
Depending on the country it’s produced in, one litre of beer requires anywhere from 61 to 180 litres of water to produce. Bringing this number down is a core objective for breweries, and making wastewater work harder is crucial to this plan.
Reducing the amount of freshwater required in brewing and distilling production requires an integrated approach to wastewater treatment. Facilities must look for new opportunities to make wastewater a valuable commodity.
An obvious opportunity is biogas production. The sugars, ethanol and soluble starch in wastewater from distillation and brewing make it perfect for biogas production with anaerobic digestion. The organic matter can be converted into biogas on-site, which can fuel facility boilers.
Facilities with no use for biogas can treat wastewater saturated in organic contaminants with a membrane bioreactor (MBR) and reverse osmosis (RO). You can use this water in machine cooling, cleaning and washing facilities.
Technologies for wastewater recovery
The primary technology used in wastewater treatment in the brewing industry is biofiltration, where bacteria consumes organic matter in the water. In bioreactors, ceramic filters can also filter suspended solids, producing a clean stream of treated water and sludge, dewatered for disposal.
Our MBRs support a flow rate up to 2,000m3/day and can run alongside other treatments like reverse osmosis for purification.
Reverse osmosis plays a crucial role in wastewater recovery, removing dissolved solids and sediments that are common with flavoured drinks. With RO, breweries can take wastewater and return it to the same quality as tap water.
The beauty of wastewater recovery and treatment is that it works alongside existing water treatment facilities that purify tap water for beverages. These systems can combine to create an integrated water production and treatment process.
Recovering wastewater, treating it, and putting it back into circulation at volume requires less energy and incurs less cost than consuming freshwater, treating it and discharging it. It’s also better for the environment and reduces emissions.
However, a few challenges include high water usage intensity, which requires industrial-capacity treatment systems, and the limited available footprint on site, which can restrict the recovery and treatment potential.
Membracon offers complete design and installation services, training, performance surveys, maintenance and service agreements. We can help wastewater work for you – call us on (0) 1902 458 501 for a chat.