Anode Cells In Electrocoating
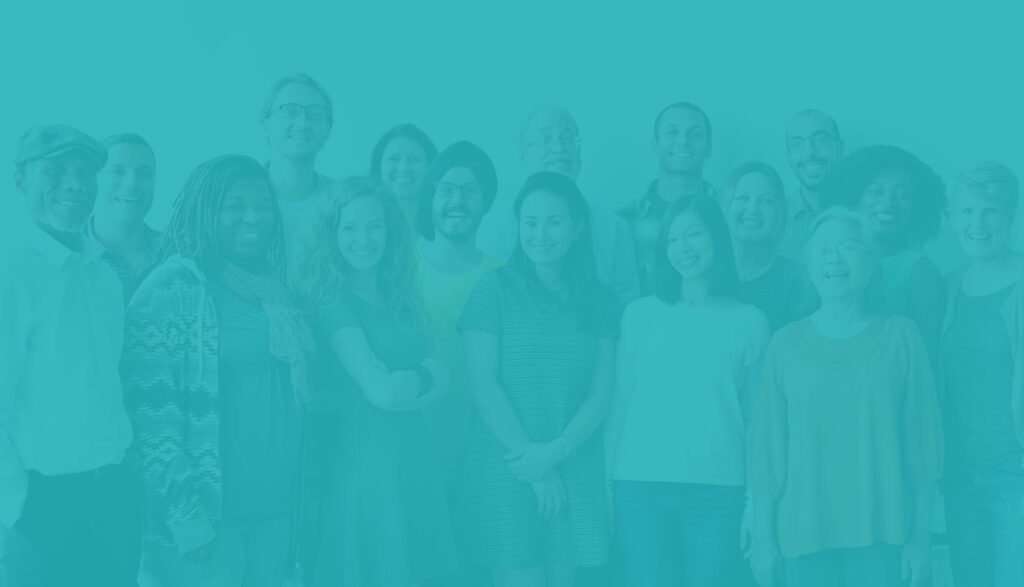
Electrocoating is a method of applying paint in a paint bath or it’s also referred to as an ecoat tank. Electricity charges the particles to deposit paint equally onto the metallic parts, the charge is determined by voltage and current.
This blog takes a look at the use of anodes in E-coating and the different types of anode cells that are available.
The Use of Anodes In The E-coating Process
Electrocoating (E-coat) paint is the base layer of paint applied to most vehicles and a variety of other products, providing corrosion resistance and physical durability. Anode cells play a dual role in the electrocoat painting process.
They acts an opposing electrode to the substrate and remove excess acid (Anolyte) generated in the paint bath during the E-coating process.
Anode cells come in a variety of forms. Historically, the main anodes used were flat cells or anode boxes. As technology progresses the introduction of tubular anodes have become a game changer.
The new style anode tubes provide bigger anode surface area in a much smaller unit. This makes it easier to control the voltage within the paint bath and to improve quality of the finished product through increased throw power.
Different Types Of Anode Cells Available
Dependent on your E-coating process, the size of your paint tank and the maximum surface area of material in the tank at any one time, the amount and size of the anodes cells you need will vary. We’ll run through the different types of Anode cells available.
Floor Cells
Floor cells are available in 1-1/2” and 2” diameters, they can be installed on the bottom of the tank to supplement side cells. In some cases the floor cell can be used to increase the uniformity of the E-coat film thickness distribution and reduce variations, dependent on its location.
Closed Top Anode Cells
For vertical or indexing conveyor systems, Membracon offers several design of Low Profile Bulkheads to reduce the necessary working height of the Anode Cell to a minimum. Also known as pressurised cells, they are offered in two primary styles, including a compression type fitting and a thread connection.
Tectron Anode Cells T1 – Small Diameter
Membracon provides a T1 small diameter Tectron Tubular Anode Cells (1-1/2”) that have the greatest membrane-to-anode ratio, providing the longest possible operational lifetimes. Small diameter Anode Cells have the most diversified anode material offering. They are ideal for job shops and general industrial applications, especially indexing or hoist type E-coat paint systems
Tectron Anode Cells T2 & T3 – Large Diameter
The larger group of Membracons Tectron Tubular Anode Cells are T2 (2 ½”), T3 (3”) and T5 (5”) and can offer automotive E-coat paint system operators an up-sized Tectron cell. This provides operational advantages of tubular cells while reducing the number of connections required. They’re designed to retrofit easily into existing E-coat paint systems.
Anolyte System
Anolyte is an integral part of the anodes system and is used on what is commonly known as a flushed anode cell. Anolyte is a solution of DI water and an acid.
The pH and conductivity of this is specified by the E-coat paint supplier. The acid to be added is normally called pH controller and is also supplied by the E-coat supplier. Once the initial solution is made up is is then automatically controlled by introducing pure water.
The function of anolyte is to conduct the charge from the anode to the paint and to carry away the acid generated in the anode cell into the anolyte reservoir.
An anolyte circulation under pressure allows adjustable flow rate for each cell individually optimising energy costs for the pumps.
Conclusion
When it comes to selecting the right Anode Cells for your E-coating process there is a wide range of choice. Feel free to get in touch, our water experts have over 100 years combined experience and are happy to recommend the best solution for your unique process.
Membracon are Members of British Water.