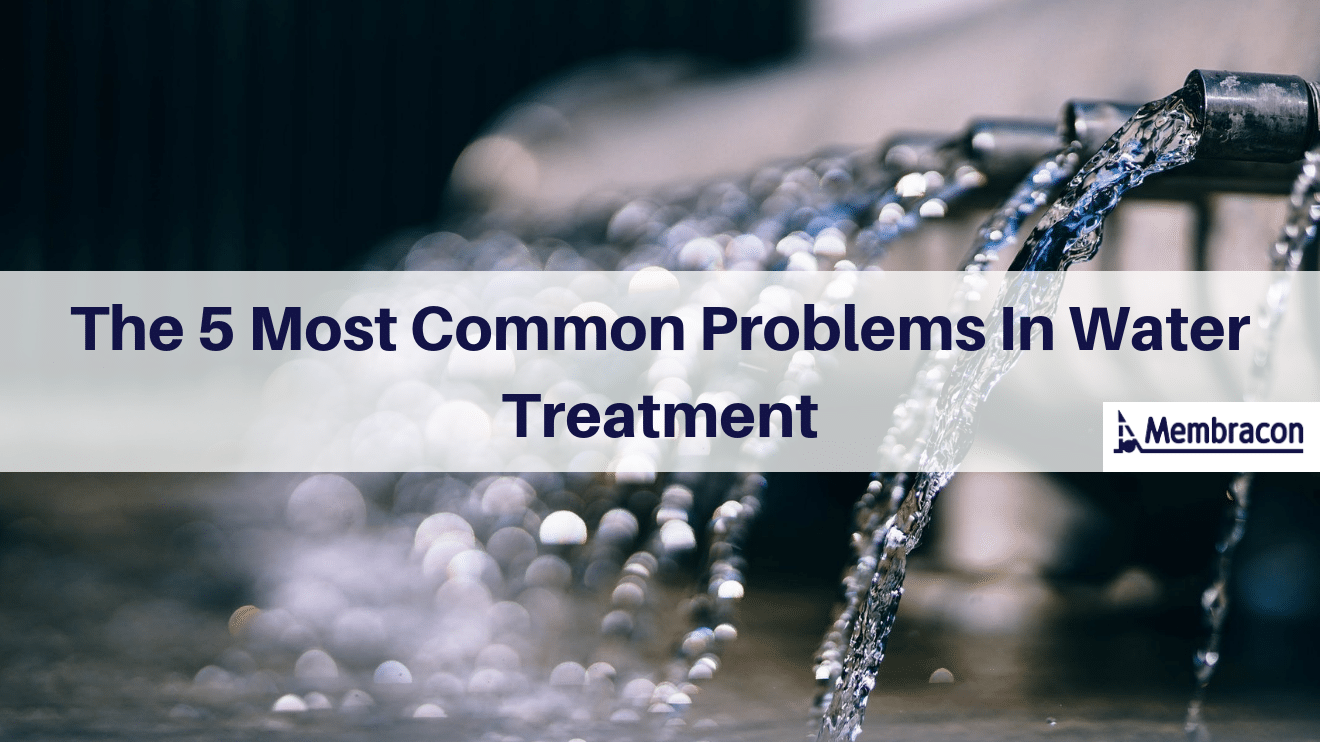
The 5 Most Common Problems In Water Treatment
The list of potential problems encountered by water treatment managers is almost endless. Often, however, it is the same ones that make the most common appearances.
Membracon are passionate about finding solutions to the most common, and complex issues encountered by water treatment experts. We have complied a list of the recommended solutions, demonstrating effective ways to overcome the challenges encountered in water treatment.
Download The Ultimate Guide To Industrial Water Filtration
The five most common problems in water treatment are:
- Training issues
- Bacteria control
- Poor monitoring and record keeping
- Equipment design and specification
- Maintenance problems
This blog post will closely examine each of these issues in detail and provide comprehensive solutions to help to resolve them.
Let’s look at each problem and its resolution in more detail…
1. Training
Most water treatment plants are small sectors in larger working systems, such as a reverse osmosis system supplying water to a 16-stage facility. Teams are large, and the process is highly technological. Managing the systems involved requires extensive, ongoing personnel training at every level within the team.
Without the right training, teams are at risk of misunderstanding the complex aspects of their sector. With quality ongoing training you can avoid this and help employees across your entire facility to flourish as industry experts with up-to-date knowledge.
Regardless of job role or position, every member of a team in a water treatment facility should have a basic knowledge on the appropriate subject matter. This includes:
- Identifying each piece of the water treatment equipment, how it works and the operating parameters.
- Understanding the preventative maintenance procedures to minimise the risk of difficulties.
- Knowing which parameters to monitor and how to identify problems.
More advanced knowledge is defined as being able to troubleshoot problems before they occur.
The most common problems in water treatment that employees are likely to encounter are:
- Scaling
- Membrane fouling
- Bacteria
- Mechanical failure
- Instrument failure
Personnel with advanced knowledge can provide on-the-job support to fill gaps in knowledge. This creates a better chance of problems being identified and resolved before they become more serious.
Most facilities rely on equipment suppliers for expert knowledge rather than internally training employees. However, by providing this high-level expert training in-house, employees will be able to quickly identify:
- Mechanical and instrument failures.
- Complex chemical, biological and bacterial problems.
2. Bacterial Control
Bacteria growth is most extensive under the following conditions:
- The presence of food for the bacteria
- Warm temperature
- A low flow rate
- The absence bacterial control solutions
Most micro-organisms feed on organic carbon-containing compounds. The ideal breeding temperature range for most water-born microorganisms is 30°- 40° (86-105°F); where the fastest growth occurs.
The concentration of the dissolved organic compounds in the feed water is measured as Total Organic Carbon or Total Oxidisable Carbon (TOC).
Micro-organisms grow best when a constant supply of food is bought in at a low flow rate, giving the bacteria time to breed.
Increasing flow rates minimises this due to the sheer force of water.
Chemicals that kill micro-organisms are called biocides.
A common practice used to be using oxidising agents, such as chlorine, as biocidal agents. However, following the introduction of stricter health and safety, environmental and chemical laws, such as COSHH, ultraviolet (UV) bacterial disinfectants are now the most common bacterial control methods utilised today.
However, there are micro-organisms that can withstand UV, making the use of UV bacterial disinfection is better for membrane filtration.
Most nanofiltration and reverse osmosis membranes have a very limited tolerance to oxidising agents.
It’s best practice to remove these oxidising agents from the feed-water upstream from the membrane unit. This is done by passing the feed-water through an activated carbon bed or water softener.
Failure to remove these oxidising agents results in bacterial growth which causes membrane fouling. This reduces the flow and makes the issue progressively worse.
An example of the impacts of poor bacteria control is a Swindon based client who had issues with bacterial infections in their electrodeposition paint tank. The client, a car manufacturer, subsequently experienced poor finishes on their products, undermining their brand’s authority.
After extensive investigations, it was found that the source of the infection stemmed from carry over on the parts from the rinse process.
The only solution was to dose this rinse section with a biocide to reduce the bacterial growth.
In consultation with Membracon’s technical team a system of UV units was suggested which would eliminate the bacterial infestation and reduce the use of biocide in the system.
Once installed and commissioned, tests were performed to ascertain the performance of the units with tremendous results.
The bacterial build-up was hugely reduced without the addition of any chemical biocides and, as a result, the client is now implementing the system throughout their entire global operation.
3. Monitoring and Record Keeping
Many water treatment systems don’t have enough instrumentation to check all the parameters to catch problems at their most preventable or reversible stages.
Even where the instrumentation is adequate, many facilities do not record the data correctly to allow them to see patterns in the data or plan preventative procedures.
It may seem like if you have excellent feed water combined with an excellent membrane unit and pre-treatment design, that the system operates on its own and looks after itself.
However, this is not always the case. It is vital to monitor certain parameters, such as:
- Silt Density Index (SDI)
- Normalised Permeate Flow (NPF)
- The pressure across each stage
- Percentage Salt Rejection (PSR) or Percentage Salt Passage (PSP)
- UV intensity
Silt Density Index is the measurement of the fouling potential of the feed water. It’s done by measuring the fouling on a membrane filter pad after feed water is passed through for fifteen minutes.
SDI means measuring may only need to be carried out monthly. However, for surface water, it should be measured once per day. The data should then be recorded and graphed weekly to allow you to see emerging patterns.
Normalised Permeate Flow is the measurement of membrane units’ performance now, versus the performance when it was new.
NPF considers changes in temperature, flow rate, salt concentration and operating pressures. If the NPF decreases, it indicates the membranes scaling or fouling. If it increases, it indicates membrane damage or bypass.
Many membrane units work on pressure drop. This is a measurement of the inlet pressure into the membrane pressure vessels, minus the outlet pressure. It correlates with flow through the membranes. With high membrane fouling, there is less available space for the water to travel, causing more resistance and the pressure drop increases.
Percentage Salt Rejection measures the percentage of conductive substances that are rejected by membranes, known as a concentrate. Percent Salt Passage (PSP) is the opposite, measuring the percentage of feed water conductive molecules that pass through the membranes.
A conductivity meter measures the real-time value. 10 micro-siemens is the most common.
Just turning on ultraviolet bacterial disinfection doesn’t mean that it will work with no further attention. Water flow passing past a UV lamp requires an amount of UV intensity to give the correct disinfection dose (mg/cm²).
Monitoring the UV intensity demonstrates when the quartz sleeve is becoming fouled and providing an incorrect UV dose.
An aerospace company who we’ve worked alongside had very little monitoring systems implemented, and no records of an ion exchange system they’ve installed on their site to produce their pure water for the pre-treatment facility.
With no records or monitoring, the performance of the units dropped considerably causing issues with the pre-treatment required for the production.
Membracon replaced the granulated carbon and resins in the ion exchange and implemented better record keeping and maintenance schedule to prevent this issue in the future. Membracon’s work saved the customer thousands of pounds in downtime and prevented rejection of work because of poor quality pure water.
4. Equipment Design Specification
Industrial Water Treatment is booming. With more OEM’s (Original Equipment Manufacturer) entering the market, many of them with little experience, it’s important to understand what an ideal design specification should look like to minimise problems.
Designs must include these components:
- Conservative Water Flux Rates
- Relatively High Cross-flow Rates
- Sufficient instrumentation for adequate monitoring
- Adequate cleaning facility.
Water Flux (identified as GFD, Gallons of permeate produced, per square foot of membrane per day) is the amount of permeate that passes through the membrane area in a given amount of time.
Acceptable Water Flux rates are:
- Surface water treatment unit with adequate pre-treatment- 10-14 GFD
- Well water treatment unit with adequate pre-treatment- 15-20 GFD
- Highly pre-treated feed water, such as ultra-filtered- 20-30 GFD
To lower costs, a new, inexperienced OEM may specify fewer membrane elements and pressure vessels than a fully experienced OEM.
The consequence is the same amount of permeate being produced by less square footage of membrane causing higher GFD which causes a higher the fouling rate.
Crossflow rates refer to the rate feed water passes across the surface of the membranes. The higher the crossflow rate, the higher the shear force. This means a lower fouling rate.
To monitor these parameters, the following monitoring instruments would be required within the unit:
- Feed Water Temperature
- Feed Water pressure
- Feed Water Conductivity
- Permeate Flow Rate
- Permeate Pressure
- Permeate Conductivity
- Concentrate Flow Rate
- Concentrate Pressure
- Pressure drops between each stage
- UV Intensity
Most units have their own built-in cleaning system including:
- A cleaning tank that can hold 2 – 2.5 times the volume of water contained in the first stage pressure vessel
- An adequate mixing system for the cleaning tank so all the chemicals required for the cleaning process are dissolved prior to the cleaning process.
- A heating element, temperature indicator and controller.
- A cleaning pump that can deliver up to 40 gpm per pressure vessel of cleaning solution to each stage being cleaned, at a pressure of less than 60 psi (4 Bar).
- A cartridge pre-filtration system to remove any particulate material prior to membrane cleaning.
- A flow indicator and flow control valve for cleaning solutions.
- Inlet and outlet pressure indicators to monitor pressure drop and control flow rate.
- A sample point so that the pH, conductivity and other parameters can be monitored.
5. Maintenance
Poor maintenance of the water treatment facility can have serious implications for the performance. Poor maintenance can result in increased costs, serious damage to systems and financial losses to the clients.
It is important to have continual maintenance processes in the water purification systems because:
- Preventative maintenance schedule for changing the pre-filtration cartridges and bags helps prolong the life of the membranes within the system
- It reduces the scaling and fouling of membranes
- Money is saved because of reduction in down time of units because leaks are found and repaired faster
- Clients can predict trends in flow and pressure and pure water quality to enable the best results through keeping detailed maintenance records
- Unit stay in good condition giving the best results for the longest period of time
Conclusion
The five most common problems for water treatment can be solved through the expert management of facilities to protect the client and the facility itself from losses, damaged reputations and violations of regulations.
With the correct management of bacteria and maintenance, as well as excellent record keeping and monitoring and staff training, facilities can make use of the excellent resources available to them to dominate in their industry as water treatment experts.